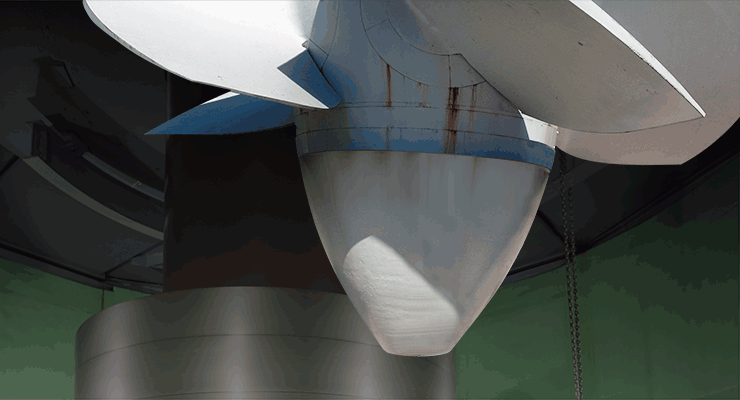
Hydropower is the largest single renewable electricity source today and provides 16% of the world’s electricity.
About Kaplan Turbines
The Kaplan turbine is one of the most commonly used turbines types in hydropower facilities around the globe. This “reaction type” propeller turbine is an evolution of the Francis turbine. It has adjustable blades and/or wicket gates (single- or double-regulation systems) to obtain optimal efficiency in different pressure/head conditions. It operates at efficiencies up to 95% in low to medium water head environments and is capable of handing high flow conditions. Typical Kaplan turbine system configurations are:
- Fixed blade (fixed pitch) propeller in combination with wicket gates
- Movable blade (variable pitch) propeller without wicket gates
- Movable blade (variable pitch) propeller in combination with wicket gates
In the double-regulated turbine systems, the runner blade position (pitch) is harmonized to wicket gate position to optimize the turbine operation to the actual water flow rate through wicket gates. The blade trunnions are supported by thrust bearings and guide bearings, which are typically cast bronze.
Kaplan runner blades have slow speed, very low frequency of oscillating movement, and remain static in most of the operating time. However the accumulated number of cycles is high, thanks to the longer operating time of turbines between repairs/overhauls. That number in the case of typical Kaplan turbine applications can achieve and/or exceed 60.000 cycles, covering the minimum to maximum oscillation value range (from 3 -45 degrees.)*
Blade Trunnion Seals & Leakage Concerns
A survey conducted among Kaplan turbine owners found that inefficient or failed blade trunnion seals cause more than 60% of Kaplan turbine leakage.**
In this post, we examine what might cause the majority of those issues in this popular turbine type. You’ll learn about some important checks to establish reliable, low leakage, worry-free sealing for trunnion seals, including:
- Taking exact turbine/blade measurements when ordering a seal
- Accounting for blade droop and variable cross section values
- Staying on top of equipment conditions
- Factoring in operational/environmental issues
- Identifying seal features designed for best reliability/ease of installation
Trends in Hydropower Industry
Hydropower technology is known as an environmental friendly, pollution-free choice for energy generation. However, it still represents a certain level of risk for the environment thanks to presence of petroleum-based oils. A high volume of oil is typically used in many of the driving/positioning functions of the fluid power system and in the lubrication of moving components of the turbine hub, as described above. Without the right care, this oil can escape into the water system.
Growing concerns over pollution has driven a move to:
- Reduce the amount of oil that is utilized in the system (replacing the low pressure servomotors by high pressure ones)
- Replace petroleum-based oils with water or bio degradable, environmental friendly fluids
- Switch petroleum-based oils with air by using electric servo motors and self-lubricated bearings
- Mitigating the risk of oil leakage that causes the downstream pollution ***
New technologies provide a more environmentally-safe operation with new or rehabilitated/upgraded units. However, for those using existing turbine units, the real focus is #4 – keeping the oil from leaking out and protecting the turbine hub against ingress of water.
Blade Droop and Seal Reliability
Due to manufacturing tolerances and running clearances of machined components, there is a certain (natural) droop of the turbine blades. But several factors can exacerbate blade droop further:
Material: The most common bearing/bushing material for runner blade trunnion is bronze. Because of the relatively low Young’s modulus (stiffness) of cast bronze, these bearings often become deformed under load, caused by the weight of the blades and by reaction force. This impacts blade droop value further.
Load: The load of vertical Kaplan turbine is the weight of the blades (depending on the turbine size, this can be couple of tons). The reaction force on the blades, generated during the operation of the turbine, causes additional load. Bearing deformation will increase the blade droop value further.
Wear: The third factor that can impact blade droop value is the wear out of blade trunnion bearings. If stable oil-film between the trunnion and bearing(s) ring is not ensured when the blade is oscillating, boundary friction occurs. In combination with high radial load (from weight of the blades and reaction force on blades), this can cause excessive wear of the trunnion/bearing assembly *
Blade droop challenges the trunnion seals—changing the original cross-section for which the seals were designed, which has an impact on sealing devices, too. Blade droop can have serious impact on performance, positive sealing, and seal life expectancy.
Such geometrical changes can lead to:
- Radial overload of the seals (where the seal cavity cross-section has been reduced)
- Radial opening of the seals (where the seals cavity cross-sections has been increased)
- Excessive deformation and friction (wear out of sealing devices), causing seal performance and sealing reliability issues
Obtain Exact Turbine/Blade Measurements
There is a wide variation in Kaplan turbines and blades when determining the seal sizes needed. Equipment dimensions also change from the original specification after years of use. For these reasons, it is important to obtain very specific equipment dimensions to optimize seal performance.
This requires taking careful equipment measurements of the:
- Blade trunnion diameter
- Stuffing box depth
- Stuffing box closing ring nose length
- Seal cavity cross section
Measure Seal Cavity Cross Section Values Around the Blade Trunnion
The natural wear of bearings and consequential blade droop values can vary blade by blade even with the same turbine. Because of this, it is important to measure these values around the circumference of the blade trunnion in various locations. In case of a typical trunnion size range 600 – 1000 mm, the recommended number of measured locations is at least 4-8 around the circumference. ****
Check & Resolve Equipment Conditions
The runner blade trunnion seals are designed to provide tight sealing between the static (stuffing box surface) and dynamic surface (trunnion). Uneven or rough surface conditions of static and dynamic hardware surfaces can have a significant impact on sealing capability and and service life.
After years of operation, the surface roughness can change and deteriorate from mechanical damages, fretting, abrasion, and corrosion from solid particles in the water.
Excessive surface irregularities and voids show where leak paths may occur when the sealing devices cannot conform to the surface irregularities.
To resolve these issues:
- Repair the surface of the stuffing box during the overhaul of the turbine. Install a stainless steel sleeve in the stuffing box for better resistance against corrosion.
- Use seal design that has multiple sealing points—insuring a tight sealing in case of corroded or damaged surfaces.
- Use a hydraulic seal made with a material that will conform to worn surfaces
Factor in Operating/Environmental Conditions
Operating conditions can have a significant impact on seal performance and service life of Kaplan runner blades.
The following are common challenges and solutions:
- Fluctuation of Turbine Pressure: Kaplan turbines operate mostly at constant or relatively constant operating conditions, just like turbine pressure (created by the water head). But head levels drop and rise, and can periodically change the pressure load on sealing devices. This fluctuation can have an adverse impact on seal performance and reliability.
- Solution: A pressure responsive, flexible seal design can handle more turbine pressure fluctuation—adjusting to actual operating conditions and maintaining positive sealing capability.
- Vibration and Cavitation: A certain level of vibration and cavitation is standard to the operation of Kaplan turbines, but it has a major impact on turbine components including runner blade trunnion seals.
- Solution: Choose a flexible seal design and elastic seal material that can respond to such impact and withstand for longer time.
- Low Water Head Schemes: Low water head can be an abrasive environment caused by high level of water contaminants, sediments, and mud.
- Solution: Use a seal with an abrasion-resistant thermoset polymer material.
Selecting the Best Runner Blade Trunnion Seal
Selecting the best quality seal helps to reduce operational and maintenance costs, lower the risk of unplanned downtime, and lessen downstream pollution. To select a high performance runner blade trunnion seal, look for the following attributes:
- Profiled lip seals: Make the sealing device responsive to fluctuation of the operating conditions.
- Flexible lip designs: Can compensate for blade droop and possible vibration of the runner blade.
- Back-to-back design configuration for a double-acting function:
- Keeps the hydraulic media and lubricant in the turbine hub
- Protects the hub against ingress of water, solid particles, and sediments
- Axial compression (stacking the seals in the groove): The static side of the seal is over-sized in an axial direction, applying compression by seal retainer ring. This axial compression locks the seal in the seal cavity, protects the seal against rotation, and provides static sealing.
- Multiple sealing point on static side of the seal: In the case of a corroded seal cavity surface, multiple sealing points can provide tighter sealing.
- Split seal design: While original equipment manufacturers typically deliver the turbines with solid runner blade trunnion seals, true split mechanical seal can greatly simplify installation on-site and reduce downtime, eliminating complicated welding or joint procedures.
- Made to order: Geometry and dimensions of the seal meet specific hardware arrangement and dimensions.
- A robust seal (high durometer seal material in combination with certain seal geometry): Helps prevent either stretching or bunching, and twisting of the seal rings during installation (problems typical with either O-Rings or traditional stacked sets).
- High performance thermoset polyurethane seal material:
- High abrasion resistance
- High tensile strength (mechanical strength of the seal material)
- Self-lubricated for low coefficient friction (less wear)
- No aging, no material degradation (estimated shelf-life 25 years)
If you would like assistance selecting the best Runner Blade Trunnion Seal solution for your specific turbine application, feel free to contact our Ask the Expert desk.
Sources:
*P. Pereira, P. Schmitt, K. Riahi and M. Müller-Brodmann – Application of self-lubricating bearings in Kaplan runner hubs 2009.
**Stevenson and Street: Living with Kaplan in the age of environment 2008.
***Roland Falkenhem, Naritoshi Nakagawa, David Havard : Technologies for Eliminating Oil in Kaplan Turbines 2011.
****Advanced Seals for Kaplan Turbines 2011 – Douglas Ell, Michael Grimanis