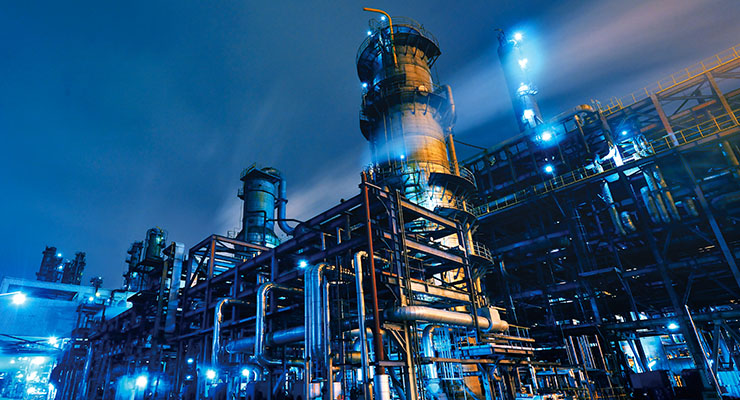
Part 2 of our series Extending the Life of Aging Fixed Plant Equipment, this post focuses on techniques and practices to reduce flange leaks and extend equipment life.
Proper gasket seating stress is important to generate the pressure drop required in sealing a flange reliably. This gasket stress needs to stay between a certain minimum and maximum value. The gasket stress is generated by tightening the flange bolts to about 30-70% of their yield strength. A sealing gap or sealing force that has fallen under a specific minimum results in failure and flange leakage.
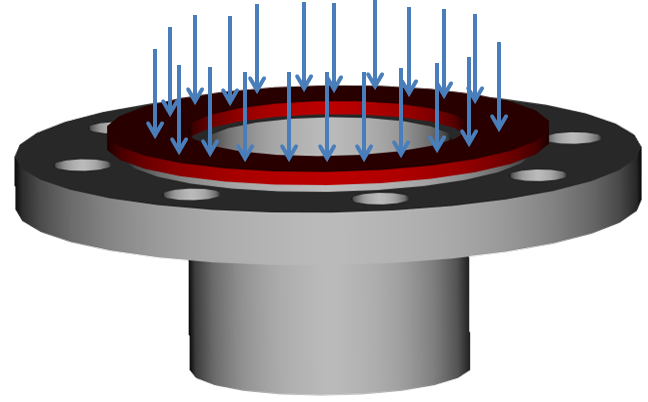
Gaskets need stress over the entire surface of the gasket
Bad flange surfaces, bad bolts, or improper tightening of bolts are common causes of flange failure. If the flange condition is bad, the flange should be replaced or repaired. Repair can be done by machining the flange or by applying a special coating (such as ARC 10 or ARC 858 depending on temperature limits). Large flanges can be machined in situ with special equipment.
Corroded bolts or plastically-deformed bolts cannot perform their function properly and will not provide sufficient sealing force on the gasket. We recommend replacing flange bolts at each gasket replacement.
Flange live loading, such as Chesterton’s 5500 or 5505H, compensates with its added elasticity for loss of gasket thickness (e.g., creep). Yielded bolts have lost their elasticity. A live loading flange disc (spring washer) is a mechanical element that helps increase the bolt’s elasticity. Bad bolting can be compensated for as well.
For a better understanding see these videos:
Correct flange tightening values are derived from theoretical calculations:
- In the petroleum industry, the method described in Section VIII of the ASME Boiler and Pressure Vessel Code is commonly used.
- In Europe, EN1591-1 is winning ground to become a reliable method to calculate the ideal bolt force on circular flanges.
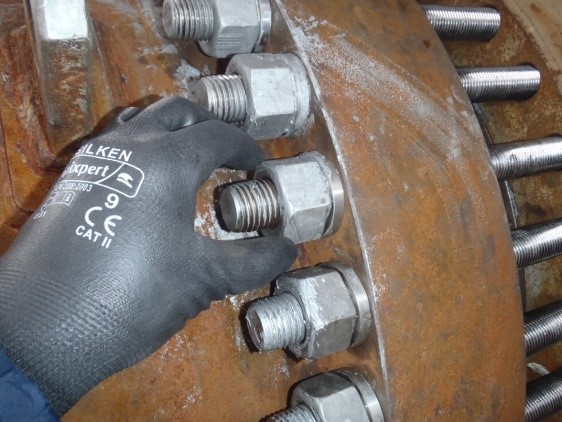
The installation of flange live loading on a shell and tube heat exchanger
Torquing
When a torque wrench is used at installation, it is important to include the lubricant’s K-factor or coefficient of friction in the torque calculations. For live loading, we typically recommend Chesterton 785 Parting Lubricant.
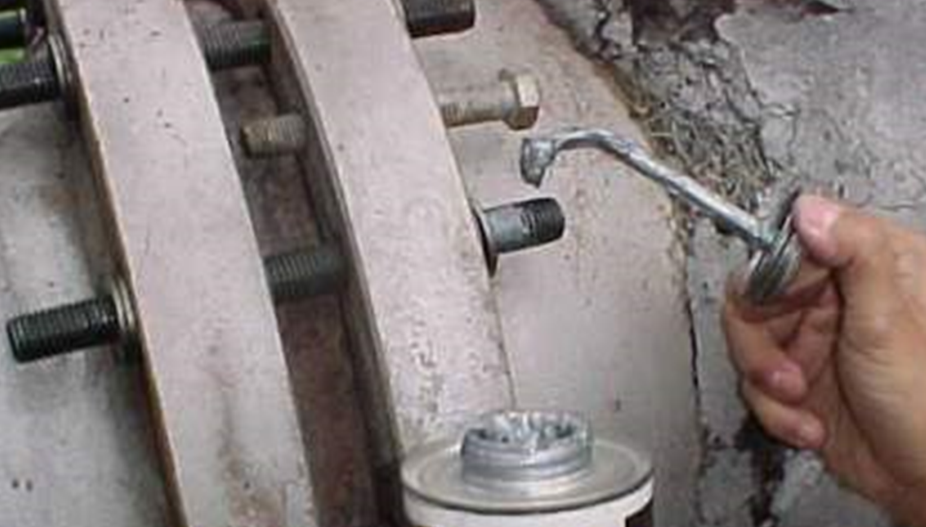
The correct stress should be established on the entire surface of the gasket. Thus all bolts should be tightened simultaneously or successively by using a tightening method that gradually build up the stress in a cross pattern. This is done by applying sequentially 30% – 60% and 100% of the final torque in a cross wise pattern; and, finally, 100% in a circular manner.
Summary
Your plant can avoid major capital investments by extending the life of the equipment that is currently in place. To accomplish this goal, it is more important than ever to follow industry best practices.
If you have specific questions, or would like to arrange a plant survey, contact your local Chesterton office.
See also:
Part 1: Cost-Effective Ways to Control Leaking Valve Stem Seals
Heat Exchanger Gaskets: Tips for Safety & Performance